Case Study: South Seniors Design a Safer Way To Transport Batteries
Posted on April 16, 2024
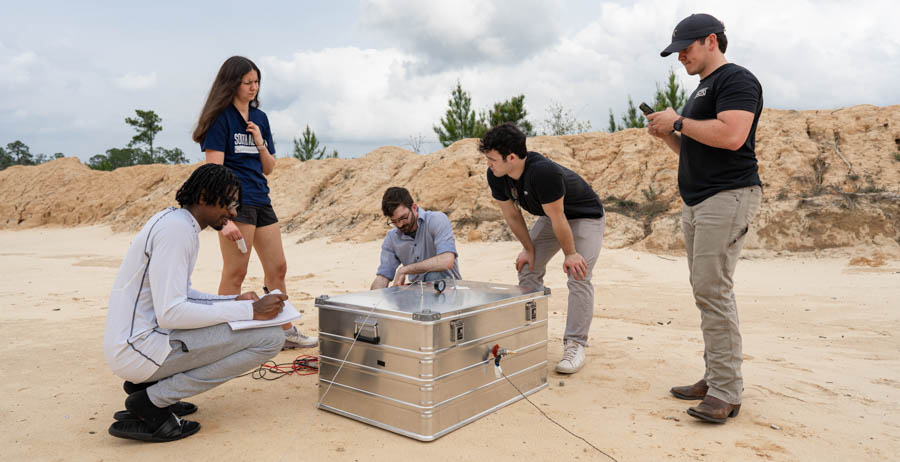
For an afternoon of testing at a firing range north of Mobile, a group of University of South Alabama seniors brought a truckload of equipment including a thermal camera, a military-grade box, $518 worth of aluminum-carbon honeycomb and a nifty cartridge heater that can quickly ramp up to 1,200 degrees Fahrenheit.
But it was a simple loose wire on a $3 battery box that produced the first hiccup. No matter. Engineers come prepared.
Out came a soldering iron — and some electrical tape for good measure.
“Better safe than sorry,” said Matthew Crump, one of five mechanical engineering students involved in a capstone engineering project to design a better way to transport lithium-ion batteries.
After just a few minutes’ delay, another student flipped the “on” switch and an accelerometer lit up. “Beautiful,” Crump said.
Drs. David Nelson and Kuang-Ting Hsiao, professors in the William B. Burnsed Jr. Department of Mechanical, Aerospace and Biomedical Engineering, received a $10,000 grant for the capstone engineering project from the Systems Engineering Research Center in New Jersey. Most of the projects are proposed by the U.S. Defense Department. Students work directly with a representative, in this case retired astronaut, much as they would with an actual business contract.
“This is something where the students can see a real-world application,” Nelson said. “There’s a specific need. They’re designing something that will actually be useful.”
Professors met with the team once a week, but students were given the freedom to experiment, make mistakes and learn from them. Independent study in a team setting. Seniors taking on new responsibilities.
“They’re the engineers on this project,” Nelson said. “They’ve shown a lot of autonomy. Our role is to be a resource and keep them from going off a cliff.”
This is the second year for this project. A previous team developed the design concept and testing methods. The possible applications extend beyond military use.
Lithium battery incidents involving air transport have been on the rise. Since 2006, the Federal Aviation Administration reported, there have been 516 incidents involving smoke, fire or extreme heat.
Many involve the overheating of passenger phones, laptops or e-cigarettes. But bulk transport incidents also have been reported. In 2022, a large shipment of lithium batteries resulted in a fire likely due to improper packaging, according to FAA data.
The box designed by Crump, along with students Paige Palazzo, Luke Andress, Devon Edinburgh and Reed Turner, can carry more than 60 pounds of lithium-ion batteries. It’s significantly larger than last year’s iteration.
The container must be able to contain fires and explosions resulting from, in technical terms, a thermal runaway event. It must also alert users if opening the protective cover would be dangerous.
For insulation, the group lined the inside of an aluminum case — one advertised as strong enough to withstand an attack from a grizzly bear — with 4 inches of ceramic wool. The wool was then draped with a welding mat. Inside, the batteries were divided by an aluminum-carbon honeycomb, or “space magic,” as Crump calls it. (Think cardboard, but extremely light and strong.)
A pressure gauge was installed to detect increasing pressure as a result of a fire or overheating. Adhesive thermal sensors were applied that change from green to red when an elevated temperature is reached.
“I think we’ve calculated it pretty well,” Palazzo said. “I think we have a good design.”
The series of tests at the firing range off U.S. 45 brought mixed results.
Critically, two tests involving shorting the batteries to initiate thermal runaway showed promise. Temperatures inside the box rose, while they stayed mostly level on the outside. The honeycomb dividers contained the thermal runaway to the shorted batteries, leaving others just inches away undamaged.
The pressure test, to see if potentially toxic air inside the box would leak, suggested there was still work to be done. With an air compressor pushing 60 pounds per square inch, the gauge on the box only rose to 10.
Modifying the box to attach the pressure gasket, and then sealing that gasket by hand, was a known question mark going into testing Palazzo said. Finding out what works, and importantly what doesn’t, is the whole point.
“Our teacher actually said you should have some unsuccessful tests, or you probably didn’t test it fully,” she said.
For two years, Palazzo, a former soccer goalie from Diamondhead, Mississippi, interned at Airbus in Mobile. “You learn a lot of skills besides just doing the engineering work — how to lead meetings and how to communicate with people,” she said.
That experience turned out to be valuable for her senior project. “I tried to get everyone in roles that followed their interests,” she said.
Crump, who is from Mobile, is in charge of client relations. He already has experience in that area as a project engineering intern with OneSubsea, an international company that produces equipment for offshore oil rigs.
“I talk to our client directly,” he said, “and I had to do that at OneSubsea as well. In project management, you need to make a plan and stick to it, regardless of what you’re doing.”
He also had familiarity with thermal runaway prior. Crump was 18 years old when he built an electric skateboard with a battery that blew up beneath him.
“I was drawing way too much current from it, and I induced the exact kind of failure we’re trying to contain with this project,” he said. “That was a very interesting experience. When I saw this project, I kind of thought back to it, and started thinking about what it would take to contain something like that.
“This is 30 kilograms of lithium batteries, so the energy density is very intensive. Imagine a hand grenade going off very slowly. How would you stop that? That kind of got my gears turning, and I knew I wanted to do the project.”