Airbus, South Team Up on Medical Masks
Posted on April 20, 2020

Engineers from Airbus and faculty from the University of South Alabama are working with healthcare workers at USA Health during the coronavirus pandemic to produce hundreds of reusable face masks for providers in clinics and hospitals.
One of the team members is John Ding, who earned a master’s degree in business administration from South and is an aircraft engineer at Airbus.
“At Airbus, we do a lot of 3D printing, we try all kinds of stuff,” Ding said. “And we’d seen on the news that people around the country were using printers to make masks. We knew we wanted to do something, but we didn’t know where, so I decided to reach out to the University.”
The first call went to Dr. Robert Cloutier, who teaches systems engineering classes for Airbus employees. The next step was a conference call with Dr. Matthew Reichert, who uses 3D printing in his chemistry research lab, and Lynne Chronister, vice president for research and economic development at South.
The COVID-19 response soon reached Dr. Benjamin Estrada, an infectious disease specialist at USA Health. Instead of face shields, which was the initial idea, he suggested making what’s called a “Montana mask,” which has a replaceable filter and a hard nylon shell that can be washed and reused.
Within just a few weeks, the Mobile Airbus engineers should be able to print 500 masks with adjustable straps. The Airbus employees work at the company’s engineering and assembly centers at Mobile Aeroplex at Brookley.
“Kudos to Airbus,” said Estrada, who’s also a professor and assistant dean at South’s College of Medicine. “They’ve done a great job for us. This will definitely help our healthcare workers be better protected.”
Nick Simpson, an Airbus project leader, was one of many who joined the mask-making project.
“I’m excited to be helping the local medical community using the skills I and other team members normally use for making things fly,” Simpson said. “We’ve had some very clever people working on this, and we are gratified to help our local medical teams where and when it’s most needed.”
Through aggressive conservation, USA Health has not faced the extreme shortages of personal protective equipment seen in some parts of the country, Estrada said, but administrators are concerned about maintaining stockpiles at University Hospital, Children’s & Women’s Hospital, Mitchell Cancer Institute and USA Health clinics.
The Airbus masks will not replace N95 respirator masks, which have run short at hospitals across the country. They do, however, meet requirements from the National Institutes of Health, and will provide an alternative to surgical masks.
“For the large majority of patient contact, we use standard surgical masks, and these are an excellent backup,” Estrada said. “The advantage is that they can be re-used, so you’re extending the life of the masks. It seems to be a very clever design. And they use a rubber window seal, so air doesn’t escape, and it’s actually a better seal than with a typical mask.”
In the chemistry department at South, Reichert is using a few 3D printers to produce tension-relief bands for the Airbus masks as well as for N95 and surgical masks. It takes about two-and-a-half hours for a printer to produce nine adjustable straps. They are also being printed at Mobile Makerspace by Ricky Green, an information technology instructor in South’s School of Computing.
At Airbus, meanwhile, there are seven 3D printers producing the larger nylon mask pieces, which take about five hours to complete. Finally, filters and bands are attached to complete the masks.
The division of labor was worked out in about a week.
“It was kind of serendipitous,” Reichert said. “I wasn’t sure what the Airbus capabilities were for 3D printing, and then they were reaching out to us. If John hadn’t had that connection to South, it would have taken a lot longer to get going.”
Ding, the Airbus engineer with the MBA from South, said many of his colleagues and co-workers volunteered to work on the project. On Friday, the Airbus and University teams working on the project made the first delivery to Estrada’s office at the Strada Patient Care Center in Midtown.
“We feel pretty good about the whole project,” Ding said. “The whole team is pretty engaged at this time.”
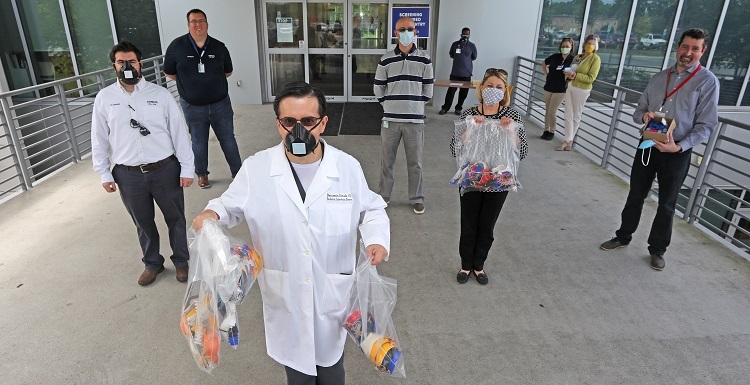